Selecting the appropriate RF connector is crucial for achieving optimal signal performance. The BNC and TNC connectors are two of the most common coaxial connectors in RF systems. This article will
will provide a comprehensive comparison of BNC vs TNC connectors, focusing on their coupling, impedance, frequency range, size, and material.
Overview of BNC Connector and TNC Coaxial Connector
The BNC connector was originally designed for military applications in the 1940s. Known for their bayonet coupling, BNC connectors are commonly used in quick mating and unmating applications. Additionally, They are available in a wide variety of configurations.
- BNC Female Connectors;
- BNC Male Connectors;
- BNC Panel Mount connectors;
- BNC Bulkhead Connectors;
- BNC PCB Mount Connectors;
- BNC Right-Angle Connectors;
- BNC Coax Connectors;
- BNC 50 Ohm and 75 Ohm Connectors;
- BNC Solder, Crimp, and Compression Connectors.
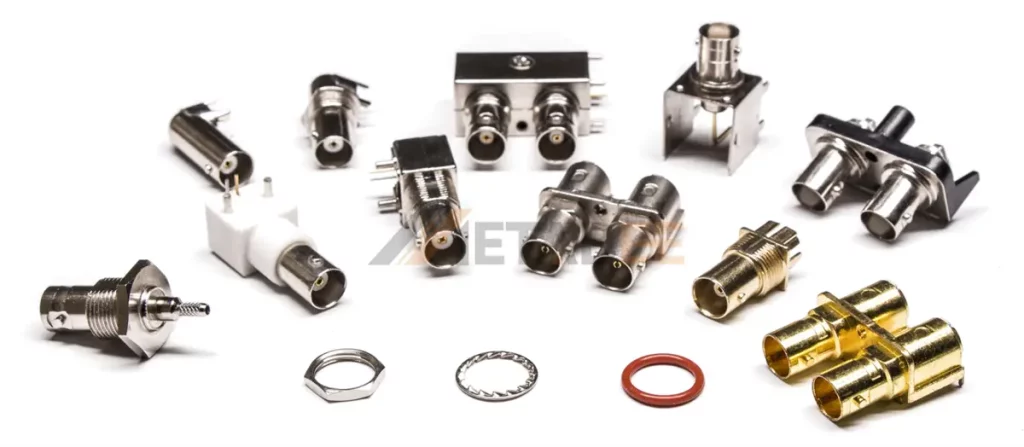
The TNC connector is a threaded version of the BNC connector. So it utilizes a threaded coupling mechanism. They are typically used for high vibration resistance or exposure to harsh environments. TNC connectors come in three main configurations: TNC male type and TNC female type, with the addition of reverse polarity RP-TNC variant for specialized uses.
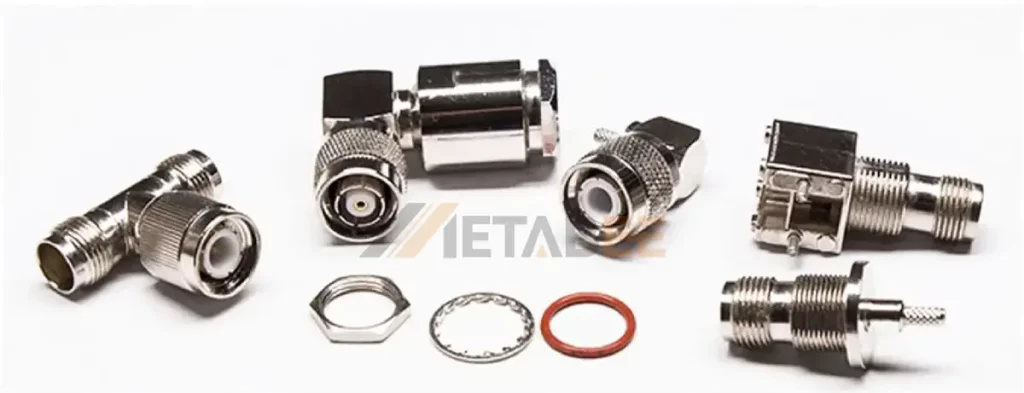
Key Differences Between BNC and TNC Connectors
BNC and TNC connectors are two types of RF coaxial connectors, but they differ primarily in their coupling mechanisms and performance characteristics.
Let’s explore the key differences between BNC and TNC connectors.
Coupling Mechanism
The BNC connector features a bayonet coupling with a simple twist-and-lock mechanism. Specifically, two lugs on the female connector engage a slot in the male connector’s shell for a secure connection. This design provides a quick, secure, and positive connection and minimizes the risk of accidental disconnects and signal loss. So it makes BNC connectors ideal for frequent connection/disconnection applications.
The TNC connector features a threaded coupling, which utilizes a thread and nut for secure mating. This design provides a more robust and stable connection that strengthens vibration and environmental resistance. Therefore, it is the first choice in high-frequency performance and durability applications.
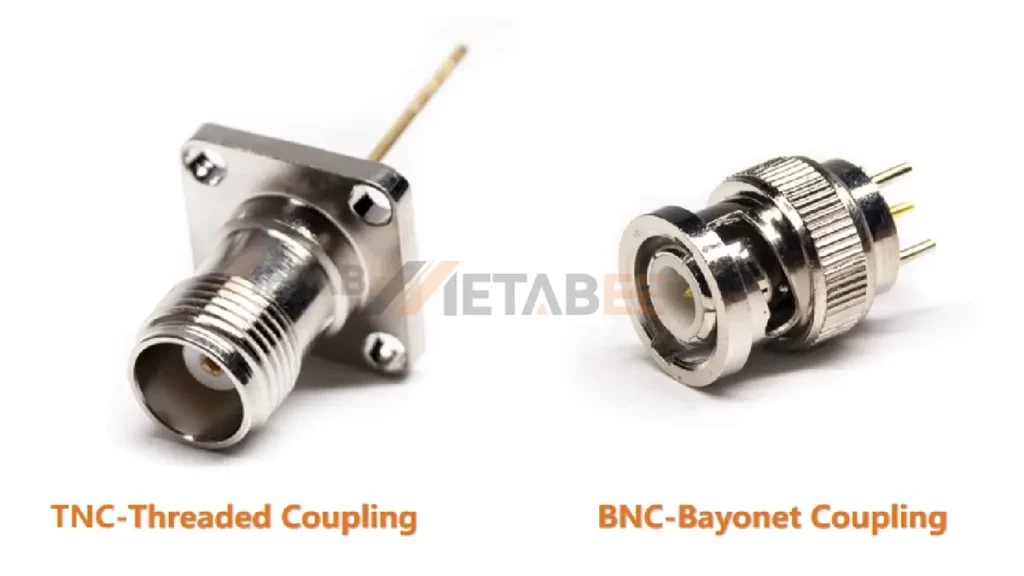
Frequency Range
BNC connectors generally support a frequency range of up to 4 GHz and are commonly used in low- to mid-frequency applications. In contrast, TNC connectors support up to 11 GHz frequency and provide better performance at higher frequencies.
Main Materials
BNC connectors commonly use copper or zinc alloy with nickel-plated for the body and copper with gold-plated for the contact material. Similarly, TNC connectors use brass with nickel-plated for the body and brass with gold-plated to enhance mechanical stability. Moreover, they both use Teflon as insulation material.
Feature | BNC Connector | TNC Connector |
---|---|---|
Body Material | Copper, Zinc Alloy | Brass |
Body Plating | Nickel-Plated | Nickel-Plated |
Contact Material | Copper | Brass |
Contact Plating | Gold-Plated | Gold-Plated |
Insulator Material | Teflon | Teflon |
Applications
BNC Connector: Commonly used in applications where quick connections are paramount:
- Broadcasting and Video Equipment;
- Telecommunications;
- Test and Measurement Equipment;
- Lower-Frequency RF;
- Medical Equipment.
TNC Connector: Preferred in applications requiring high reliability and resistance to vibration, including:
- Wireless Communication;
- Higher-Frequency RF;
- Military and Aerospace;
- GPS Systems;
- Industrial and Automation Systems.
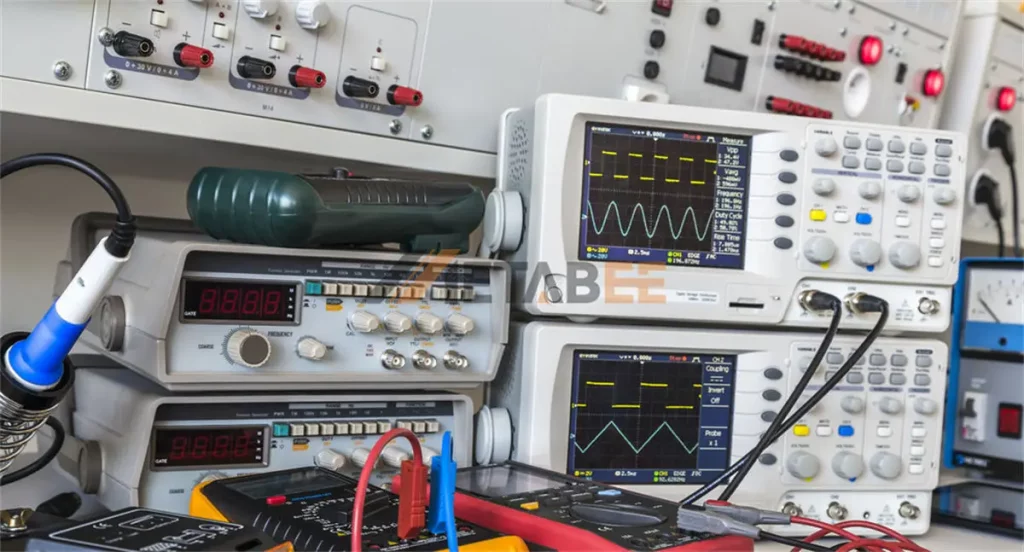
Contact Resistance
The TNC connectors have higher contact resistance compared to the BNC connectors.
The BNC connector features a maximum center contact resistance of ≤ 1.5 mΩ and outer contact resistance of ≤ 2.0 mΩ.
As for the TNC connector, the maximum center contact resistance is ≤ 3.0 mΩ, with outer contact resistance also ≤ 2.0 mΩ.
Temperature Range:
Generally, BNC connectors offer a wider operating temperature range of -55℃ to +155℃, making them ideal for applications in harsh environments.
TNC connectors are designed to operate in a temperature range of -55℃to +165℃, thus, making them suitable for a variety of consumer and industrial applications.
Size
BNC coaxial RF connectors are smaller and more compact, making them suitable for space-constrained applications. TNC connectors, while larger and bulky, offer improved durability and signal integrity due to their threaded coupling.
Price
BNC connectors are typically more affordable and widely accessible, making them well-suited for consumer and low-end industrial applications.
TNC connectors generally command a higher price due to their intricate design and enhanced durability.
Below is a breakdown of the main differences between the two connectors:
Feature | BNC Connector | TNC Connector |
---|---|---|
Coupling Mechanism | Bayonet Coupling | Threaded Coupling |
Frequency Range | DC – 4 GHz | DC – 11 GHz |
Body Material | Cooper, Zinc Alloy | Brass |
Body Plating | Nickel-Plated | Nickel-Plated |
Contact Material | Copper | Brass |
Contact Pating | Gold-Plated | Gold-Plated |
Center Contact Resistance | ≦ 1.5 mΩ Max | ≤ 3.0 mΩ Max |
Outer Contact Resistance | ≦ 2.0 mΩ Max | ≤ 2.0 mΩ Max |
Temperature Range | -55°C to +155°C | -55°C to +165°C |
Price | More Affordable | More Expensive |
Size | Smaller and More Compact | Larger and More Bulky |
Applications | Broadcasting and Video Equipment, Telecommunications, Test and Measurement Equipment, RF (lower frequency), and Medical Equipment. | Wireless Communication, RF (higher frequency), Military and Aerospace, GPS Systems, Industrial, and Automation Systems. |
Similarities Between BNC and TNC Connectors
Despite their differences, BNC and TNC connectors share several common characteristics:
Feature | BNC and TNC Connector |
---|---|
Structure and Components | Body, Center Contact, Insulator |
Standard | MIL-STD-348, IEC-61169 |
Body Plating | Nickel-Plated |
Contact Plating | Gold-Plated |
Insulator Material | Teflon |
IP Rating | IP65 |
Impedance | 50 Ohm / 75 Ohm |
VSWR | Straight Type ≦ 1.3GHz Right Angle Type ≦ 1.5GHz |
Dielectric Withstanding Voltage | 1500 V RMS |
Working Voltage | 500 V RMS |
Insulation Resistance | ≥ 5 × 103 MΩ (Megohms MIN.) |
Mating Durability | ≥ 500 Cycles |
Contact Retention | 6 lbs MIN |
Coupling Nut Retention | 100 lbs. min. |
Vibration | MIL-STD-202 Meth. 204 |
Corrosion resistance | MIL-STD-202 Meth. 101 |
A Step-by-Step Selection Guide Between TNC and BNC Coaxial Connectors
When selecting between BNC and TNC connectors, several factors should be considered to ensure optimal performance and reliability in your application. Below are key considerations to guide your decision-making process:
Step 1: Determine the Frequency Requirements
- BNC: Primarily suitable for lower frequencies, typically up to 4 GHz.
- TNC: Designed for higher frequencies, often extending into the microwave range (up to 11 GHz or more).
If your application operates at higher frequencies, TNC connectors are the preferred choice.
Step 2: Evaluate the Environmental Conditions
- Vibration: TNC connectors, with their threaded coupling, offer superior resistance to vibration.
- Moisture and Dust: Both BNC and TNC can be designed with IP65 for environmental protection.
For applications in harsh environments with vibration or moisture, prioritize TNC connectors or IP-rated versions of either type.
Step 3: Consider the Connection Mechanism
- BNC: Bayonet coupling allows for quick connect/disconnect, ideal for frequent mating.
- TNC: Threaded coupling provides a secure and robust connection, suitable for long-term reliability.
Choose BNC for applications requiring rapid connections and TNC for applications requiring secure, stable connections.
Step 4: Assess Size and Space Constraints
- BNC: Smaller and lighter, making it a better choice for compact devices or applications with limited space.
- TNC: Slightly larger and heavier due to its threaded design.Ensure your device or system has enough space to accommodate TNC connectors.
If space is limited, carefully review the dimensions of specific connector models.
Step 5: Check Impedance Requirements
- Both BNC and TNC connectors are available in 50 ohms (standard for RF applications) and 75 ohms (used for video and broadcast applications).
Ensure the connector’s impedance matches your system’s requirements to avoid signal reflection and loss.
Step 6: Evaluate Cost and Budget
- BNC: Generally more cost-effective and readily available, making it a good choice for budget-conscious projects or applications where high performance is not critical.
- TNC: More expensive, especially for high-performance or specialized models. Choose TNC if your application demands higher performance and reliability.
Step 7: Review Application-Specific Needs
- BNC: Commonly used in video surveillance (75 ohms), test and measurement equipment, and general-purpose RF connections.
- TNC: More frequently used in RF applications, including wireless communication (5G, 4G, Wi-Fi) and antennas, military and aerospace systems, satellite and radar systems, and high-vibration industrial environments, where a more robust connection is required.
Step 8: Make a Decision
- Choose BNC:
– Your frequency range is 4 GHz or lower.
– You need quick and easy connections.
– Environment is low-vibration and indoor.
– Budget is a primary concern.
- Choose TNC:
– The frequency range is up to 11 GHz.
– Need a secure, vibration-resistant connection.
– Application is in a harsh or outdoor environment.
– Performance and reliability are critical.
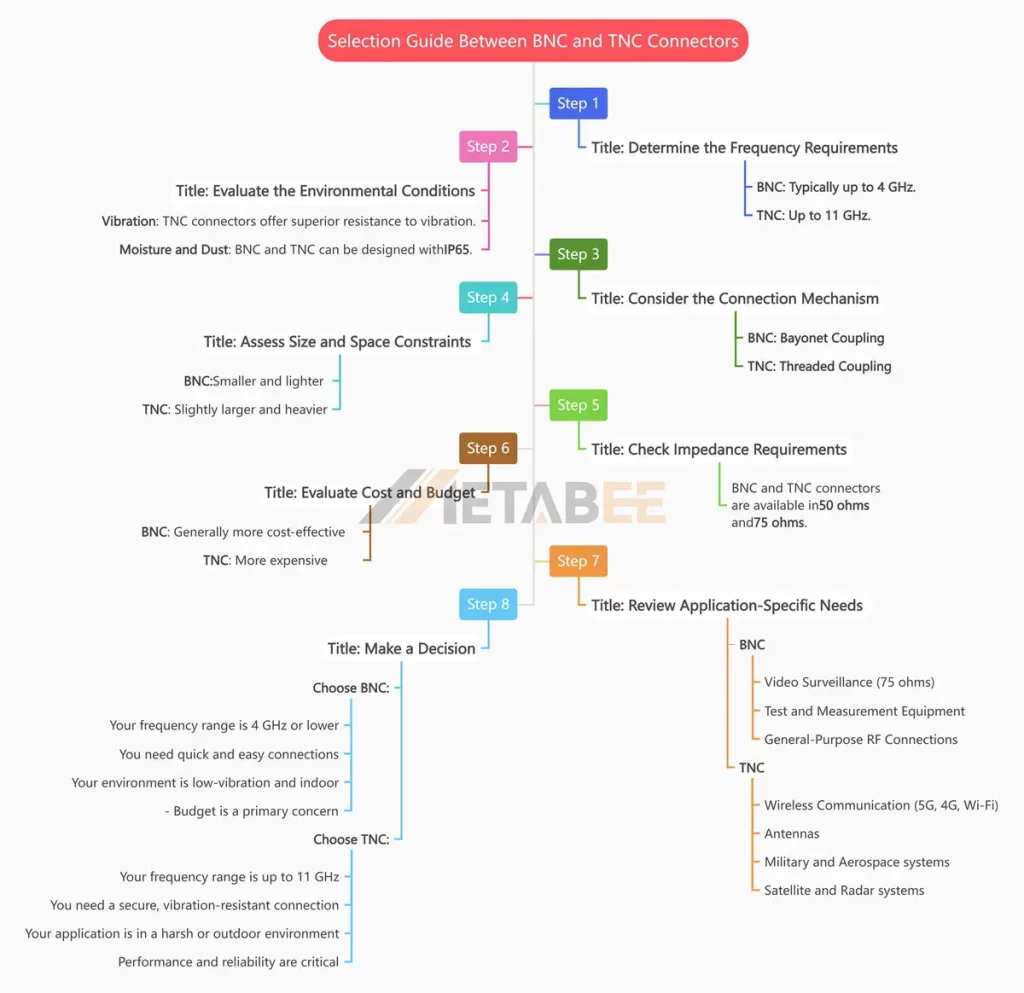
Still unsure whether a TNC or BNC connector best fits your needs? Our expert technical team is ready to provide personalized guidance. Contact us today for assistance.
Conclusion
In summary, these two connectors are essential components in RF and microwave applications, each offering unique advantages. BNC connectors are ideal for quick-connect applications, limited space, priority cost efficiency, and low-frequency environments where frequent connections and disconnections are needed. On the other hand, TNC connectors provide more secure and stable performance in high-vibration environments and higher frequency ranges.
When choosing between BNC and TNC connectors, it is crucial to consider factors such as frequency requirements, environmental conditions, connection mechanisms, size constraints, impedance matching, and budget. By carefully evaluating these aspects, you can select the connector that best suits your application, ensuring optimal performance and reliability.
Related Products
For further exploration, consider reviewing related products and accessories:
They include:
Pingback: What is an N-type connector? A Deep Dive - MetabeeAI